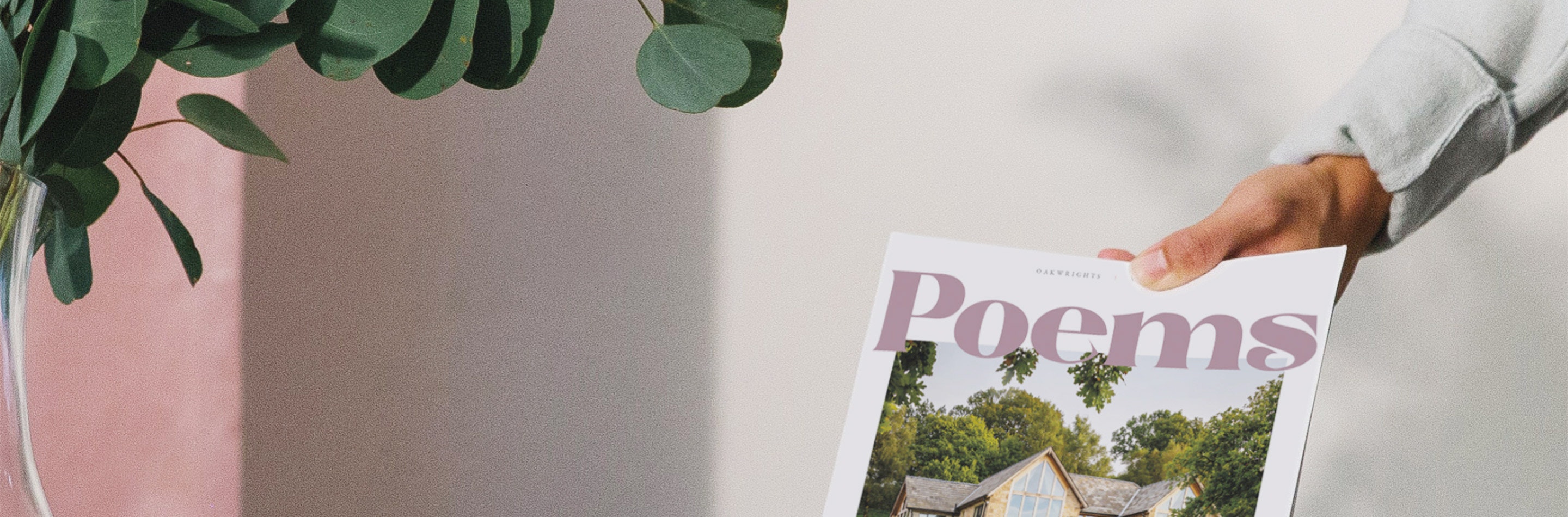
Latest news from Oakwrights
Filters
- 1
- 2
- 3
- 4
- 5
Latest news from Oakwrights
Filters
Contact us
Want to discuss plans for your own oak frame project, organise a visit to our workshops, book a stay in our show home or just gain some advice? Please get in touch.