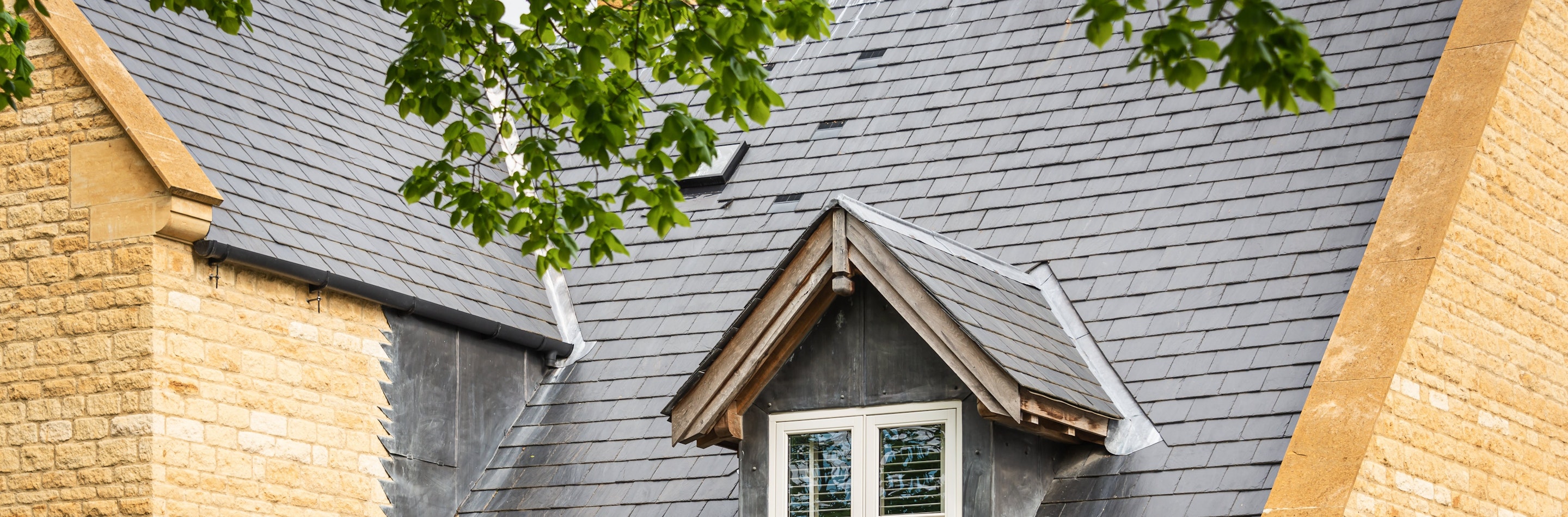
Our premium pre-insulated panel systems
Discover the pinnacle of efficiency with our WrightWall and WrightRoof
pre-insulated panel systems.

Building 'the wright way' with our premium pre-insulated panel systems
Building 'the wright way' with our premium pre-insulated panel systems
Throughout the design process, we use the same innovative software employed to design your oak frame as your panel system. Whether you choose our WrightWall and WrightRoof system, or our WrightWall and WrightRoof Natural system, your panels will be fabricated in our workshops, which reduces time on-site while ensuring precision and quality control.
Which panel system is Wright for me?
Key features and benefits | WrightWall/Roof | WrightWall/Roof Natural | Precision engineered. Designed and produced to fit perfectly around your oak frame. | Vertical service battens and custom service voids for trouble-free first fix. | Bespoke panel sizes. | Exceeds Building Regulations airtightness and insulation requirements. | Pre-fabricated in dry, clean conditions for the highest quality panel build. | Low household energy bills. | Delivered and assembled by our highly experienced Site Foreman and Site Crew. | Airtight tape installed by our Site Crew to seal panel joints. | Self-supporting without structural oak frame. | Enhanced exterior noise reduction. | Passivhaus levels of insulation possible. | High-tech eco insulation protecting against the cold, heat, moisture. |
---|
Our sustainable process
Our sustainable process
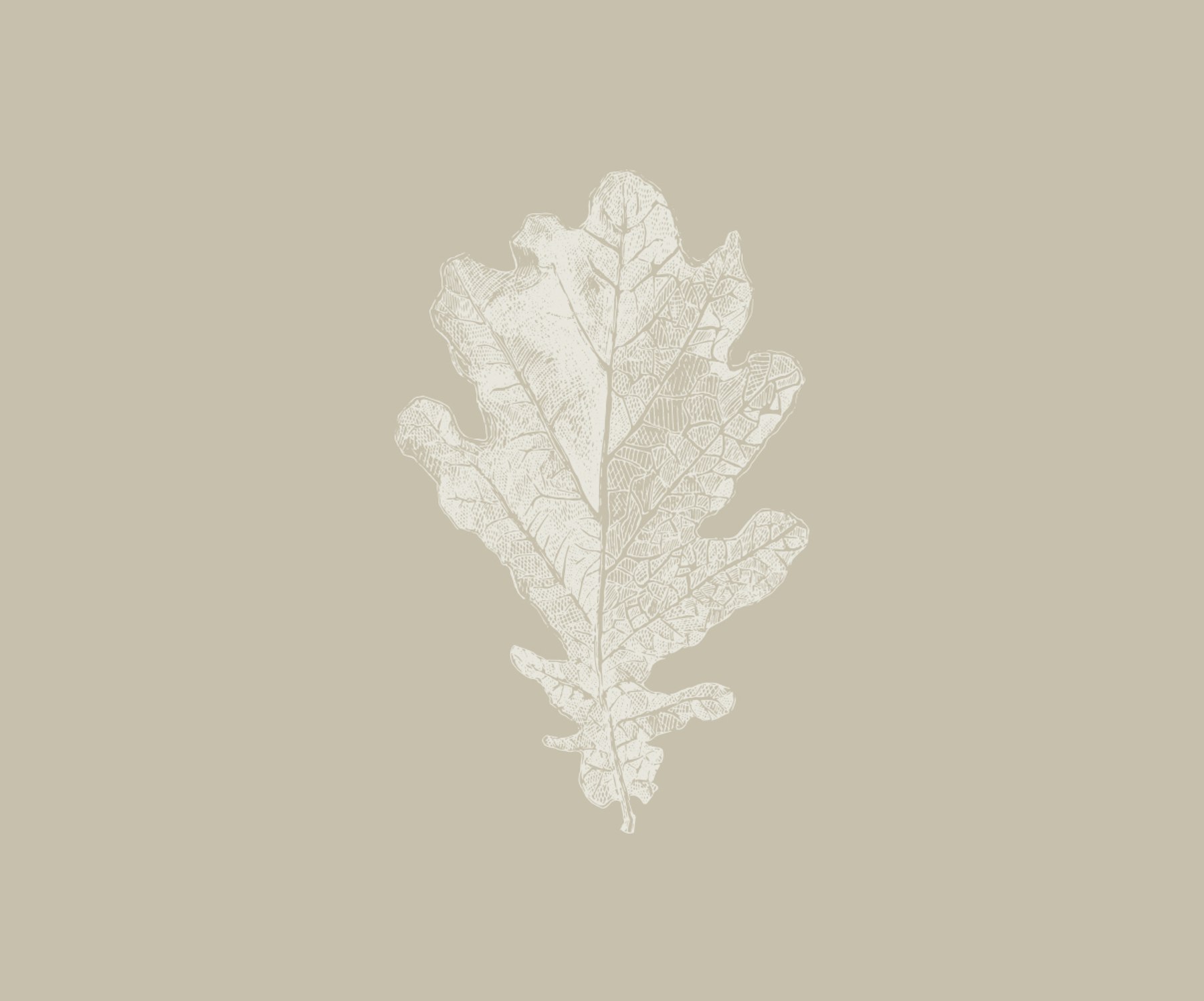
A selection of our builds
Homes built with energy efficiency at the forefront
Homes built with energy efficiency at the forefront
From the experts
From the experts